5’’
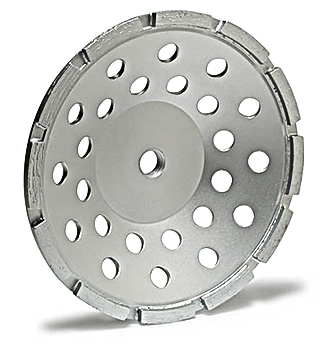
Achieve superior surface grinding and polishing results with the versatile Single Row Cup Wheel , featuring a Single Row of diamond segments for efficient material removal and refined finishing. Designed for concrete, stone, and masonry surfaces, it delivers precise grinding and polishing outcomes. Compatible with angle grinders, floor grinders, and hand grinders, it serves various applications including concretesurface preparation, surface leveling, and coating removal. Engineered with durable construction and high-quality diamond segments, the Single Row Cup Wheel ensures prolonged performance, offering contractors and DIY enthusiasts outstanding value.
The Single Row Cup Wheel is a crucial tool for surface grinding and polishing, featuring a single row of diamond segments for efficient material removal and seamless finishing. Primarily designed for concrete, stone, and masonry surfaces, it ensures precise grinding and polishing outcomes. Its versatile design accommodates angle grinders, floor grinders, and hand grinders, making it suitable for concrete surface preparation, leveling uneven surfaces, and removing coatings. Crafted with durable construction and high-quality diamond segments , this wheel delivers long-lasting performance, catering to the needs of both contractors and DIY enthusiasts with exceptional value.
Single Row diamond Cup wheels offer precision and efficiency in surface grinding, delivering uncompromising performance for diverse grinding needs. Designed to excel on various materials, these wheels provide contractors with a versatile, efficient, and durable solution for tough jobs across construction and fabrication projects.
Advantages:
Lightweight Maneuverability: Effortless handling and increased productivity due to the lightweight design, reducing worker fatigue and leading to faster completion times.
Optimal Heat Dissipation: Engineered with a venting hole design for efficient heat dissipation during operation, allowing prolonged grinding sessions without sacrificing performance or safety.
Dry Cutting Convenience: Specifically designed for dry use with electric power tools, simplifying the grinding process and eliminating the need for water control, offering convenience on the jobsite.
Compatibility Options: Available in non-threaded (7/8” - 22.2mm) or threaded (5/8”-11UNC) arbor options for seamless integration with existing power tools.
Targeted Applications:
Concrete Leveling and Smoothing
Masonry Work and Shaping
Stone Finish Work and Polishing
Surface Preparation and Clean-Up
Technical Parameter | ||||
Item No. | Diameter | Segment Number | Arbor | |
inch | mm | |||
HNSSCW040 | 4’’ | 110 | 8 | 7/8’’ or 5/8’’-11UNC |
HNSSCW045 | 4-1/2’’ | 115 | 9 | 7/8’’ or 5/8’’-11UNC |
HNSSCW050 | 5’’ | 125 | 10 | 7/8’’ or 5/8’’-11UNC |
HNSSCW070 | 7’’ | 180 | 12 | 7/8’’ or 5/8’’-11UNC |
How to Buy
Request an Equipment Quote
Ready to buy stuff from Flexible,Request a quote now.
Buy
Browse Parts and equpments on our store
Reviews
FAQ
Q: What are the most common types of drilling method?
Here are the five common types of oil drilling techniques. 1. Cable Drilling. 2. Directional Drilling. 3. Electro-Drilling. 4. Rotary Drilling. 5. Dual-Wall Reverse- 6. Circulation Drilling.
Q: How deep can a drill rig go?
Depending on the rig type, offshore rigs are rated to drill in water depths as shallow as 80 feet to as great as 12,000 feet. The greatest water depth a jackup can drill in is 550 feet, and many newer units have a rated drilling depth of 35,000 feet.
Q: What is the process of oil exploration?
Oil and gas exploration encompasses the processes and methods involved in locating potential sites for oil and gas drilling and extraction. Early oil and gas explorers relied upon surface signs like natural oil seeps, but developments in science and technology have made oil and gas exploration more efficient.
Q: What are the positions on a rig?
Diver – Some rigs require the use of divers to maintain the underwater equipment. Driller – Heads up all operations related to the drilling equipment. Electrician – Maintains and repairs all electrical systems onboard the rig. Floorman – Provides general support to the rig's drilling operations.